Innovator Creates Repairable AirPods Pro Case Using USB-C iPhone Technology
Ken Pillonel, a robotics engineer famous for his innovative USB-C iPhone and AirPods, has recently unveiled his latest endeavor. This talented modder has successfully disassembled Apple’s AirPods Pro case and constructed a personalized version that can be easily repaired. Pillonel is generously offering the design for free, enabling resourceful DIY enthusiasts with engineering skills to create their own custom AirPods Pro case.
Pillonel has already tackled the AirPods Pro with a custom replaceable printed circuit board (PCB). However, his new project attempts to deconstruct the entire case of the headphones and offers a complete plan for others to do the same – with 3D printed parts and a few (cheap) afterparty parts. “Most gadgets are designed without repairability in mind, unlike the durable technology of the past that seemed built to last,” Pillonel wrote, noting that iFixit gave the second-generation AirPods Pro a dismal zero repairability rating. “It is troubling to see design choices such as non-replaceable batteries, bonded components and lack of transparency in public information leading to the rise of ‘fast electronics’.”
In response, the engineer embarked on this latest project “to show how one of the most popular gadgets of the moment—Apple’s AirPods Pro—could have been made easily repairable with little effort.” His stated goal is to inspire consumers and multi-billion dollar companies (ahem, Apple) to treat technology less like a locked-in disposable commodity and more like something to tinker with, learn from, and—with the right skills—fix. Of course, the key component uses screws and nuts instead of glue to create a temporary housing that you can open and fix on the road.
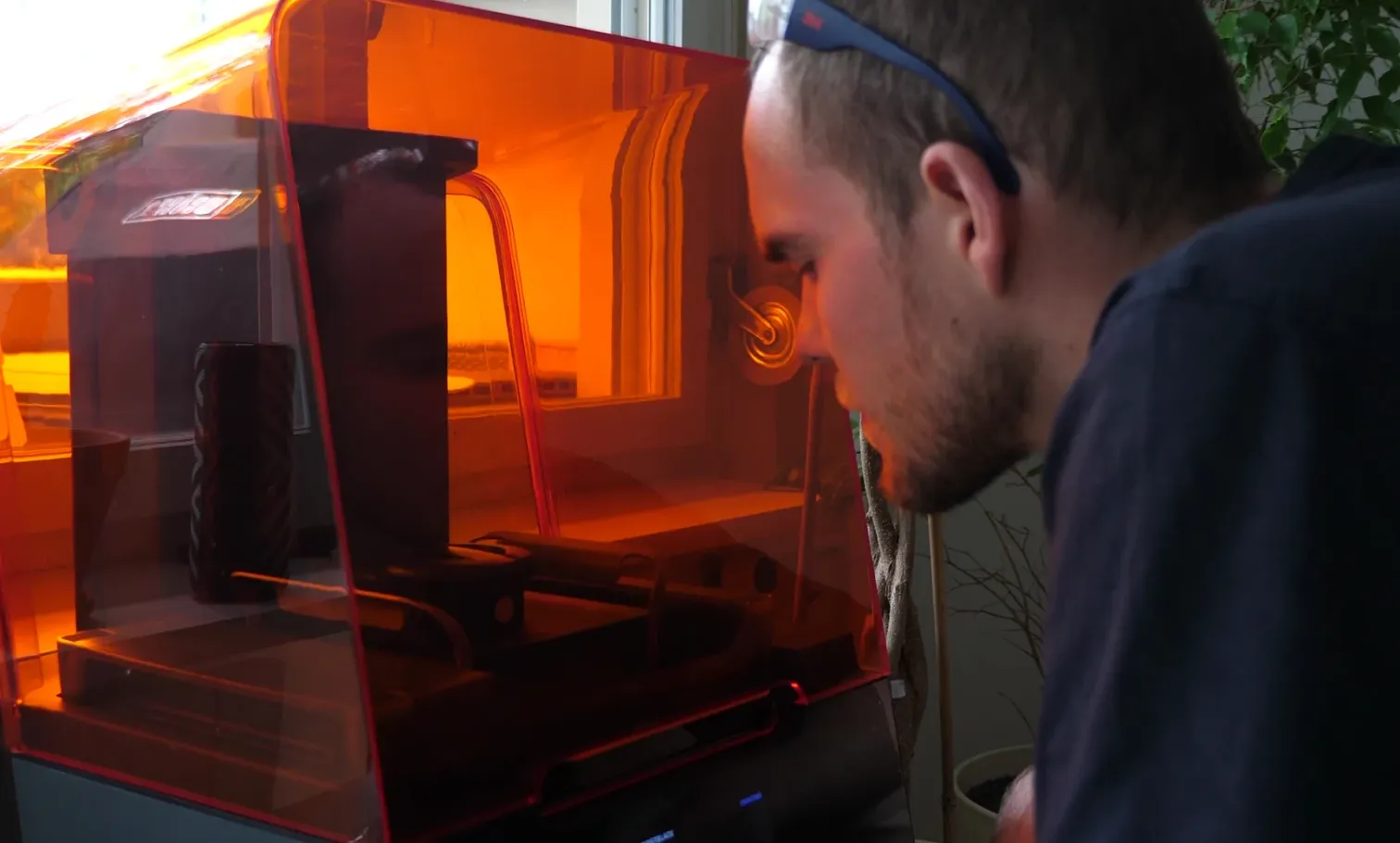
Pillonel says this was one of his most challenging custom projects to date, as he had to create accurate scans of every component of the case. As he explains in the video below on his YouTube channel, some parts of the case proved particularly difficult with complex curves that simple thickness and basic 2D scans couldn’t capture. He even detailed his quest to find the right spring-loaded Contact Pins to load the hubs and an inexpensive 3D scanner to record some of the more oddly shaped parts. I recommend the Speedwatch to anyone interested in durability and the nuts and bolts behind iconic consumer technology devices. (Keep in mind that this kind of tinkering will void your warranty, and you should probably only try it if you’re experienced in repairing electronics.)
“I’m excited to make these repairable designs available to the public at no charge, encouraging individuals and manufacturers to prioritize repairability in their product development,” Pillonel wrote today. “Together we can work towards a circular economy that not only minimizes electronic waste but also promotes a culture of conscious consumption and responsible technical innovation.” You can check out Pillonel’s design and spare parts store on his website.